S-Bond® active solders enable ceramic to metal bonding and sapphire to metal bonding as well as to each other. S-Bond alloys have active elements such as titanium and cerium added to Sn-Ag, Sn-In-Ag, and Sn-Bi alloys to create a solder that can be reacted directly with the ceramic and sapphire surfaces prior to bonding. S-Bond alloys produce reliable, hermetic joints with all metals…including steel, stainless steels, titanium, nickel alloys, copper and aluminum alloys.
Ceramic to metal bonding is seeing increased application for use in sensors, electronic packaging and in power electronics. From sensor windows where quartz and/or sapphire (single crystal aluminum oxide which is transparent) to aluminum oxide or aluminum nitride are used as insulating bases where high voltages need to be isolated. However, “mother nature” has handed engineers a double set of problems… 1) ceramics do not like to be directly wetted (molten metal layers adhering) and 2) ceramics and metals have largely different coefficients of thermal expansion (CTE). These two problems have limited the application ceramics in combination with metals for many years.
Ceramic to metal bonding historically has been done one of two ways 1) adhesives or 2) soldering or brazing… where the ceramic component has to first have a metal layer applied (vacuum metallizing, Mo-Mn oxide + plating process or active brazing). Solder or braze attachment has been preferred in many cases over adhesives since solders (or brazes) are metals and are thermally conductive and are hermetic and do not degrade of pass moisture. When considering braze attachment of ceramics to metals, the issue of CTE is limiting since brazes melt over 840°F (450°C) and upon cooling the solidified joint stresses can fracture or distort a part. Many times brazed ceramic-metal joints will require the use of a low CTE metal such as Kovar®, Invar® or Molybdenum. On the other hand, solders, by definition melt and thus join at temperatures below 840°F and normally closer to 480°C (250°C). As such, soldered joints are much better at joining ceramics to metals since the joining stresses are much lower due to solidifying from much lower temperatures than brazed joints. The caveat with conventional solders remains that an adherent metal layer must first be placed on the ceramic surface then followed by a solder-flux process to disrupt the oxides that form on the metal and metal coating on the ceramic as they are heated on the solder joining process.
S-Bond active solders solve many of these joining issues, these alloys:
- Directly bond ceramic-metal joints without the use flux.
- Without pre-coating steps, eliminating multiple step coating processes, and
- At temperatures below 400ºC, preventing distortion and softening of metals and preventing ceramic fracture.
The joints produced are:
- Hermetic, passing < 10-9 atm-cc/ sec
- Strong (> 5,000 psi shear)
- Ductile, based on Sn-Ag or Sn-In alloys
- Thermally conductive
S-Bond Processing
Two different processes can be used in ceramic to metal bonding. One method is the “mechanically activated” joining at near the S-Bond melting temperature, (e.g. for S-Bond 220, that is 250ºC). This is done by spreading, rubbing, or brushing the molten alloys onto heated surfaces and assembling “hot” in a way that the S-Bond alloy surfaces are agitated sufficiently to break the thin oxide skins that form while molten. Such joints on ceramics and many metals are adhesive, but have no chemical bond. An example of the bond is shown, below. S-Bond alloys do bond, but the joint strengths are nominally below 3,000 psi in shear. The figure to the right illustrates the adhesive nature of the bond.
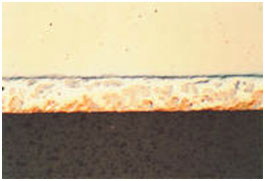
Another S-Bond joining process is thermally activated using a proprietary process, which prepares the ceramic and sapphire surfaces and develops a chemical bond to the surface, through reactions of the active elements in S-Bond alloy. These joints start with an elevated temperature treatment in a protective atmosphere furnace with S-Bond alloy placed on the ceramic surfaces to be joined. At the elevated temperatures, the active elements in S-Bond react with the ceramic to develop a chemical bond, as shown in the figure below.
This chemical bond and the S-Bond layer in a subsequent joining step provides a much higher level of joint strength and creates high performance ceramic-metal joints that are better than most brazed sapphire and ceramic to metal joints made by the multi-step Mo-Mn and plating processes.
S-Bond joint micro-structures shown in the figure to the right illustrates that a chemical bond has been created between the alumina (Al2O3) and the S-Bond alloy.
S-Bond joint shear strengths, using the elevated temperature S-Bond metallization procedure exceed 7,000 psi and are resistant to thermal cycling from -50 – 150ºC.
S-Bond joins sapphire, ceramic and metal surfaces without flux or plating and the process is much more tolerant of joint variations due to the nature of the S-Bond alloys’ high surface tension. S-Bond joining does not use chemical fluxes that must be cleaned up or could etch metallic components, leaving cosmetic defects.
Examples of Sapphire and Ceramic Metal Components

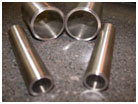

Please contact me and add your application to the growing list of successful S-Bond ceramic-metal bonded components.
S-Bond joining meets the needs of many applications where sapphire and/or other ceramics need to be joined to metals. The figure below illustrates other applications of S-Bond joining. Thermal management and heat sinks, C:C composites to aluminum, Si-die attach, quartz to brass sensor housings, MEMS sensors on BeO to brass and foamed metals.
20 Responses
Hello
I’m interested to learn more about your ceramic/metal bonding methods. Specifically I need to bond ceramic to aluminum but without exceeding the ceramic’s (PZT) curie temperature ( about 350C) in the process.
01590 613407
G Evans
Gill Technology
Thank you for your interest. We will contact you directly.
I’m interested to learn more about your ceramic/metal bonding methods. Specifically I need to bond ceramic to mild steel curie temperature ( about 150C) in the process.
Hello
I’m interested to learn more about your ceramic/metal bonding methods. Specifically I need to bond alumina to steel by friction welding method.can you help me?
very interested – do any of your products allow for electrical conductivity.?
I am looking for solution to join a ceramic pipe (small inner dia) to a metal pipe (bigger inner dia) using a ceramic paste. I am looking for good joint torque strength and min gas leake through the joint. Do you have a solution for it.
Thanks
AP
please suggest how to join the Alumina ceramic metal and stainless steel.
I need to know more about ceramic on metal and how is it applied on metal parts.
How to joint the ceramic with copper,and attached component at top copper.
Hi,
I whish to Bond a machined ceramic that will withstand a water pressure (60psi) to a copper substrate. The bonding interface must not be “affected” by an EM field of 175 kHz .
Thank you
We want to bond a ceramic cylinder {1.003″ diameter x 0.71″ long AlOx3 ( 96% pure) } inside a SS316 Block with a 1.007″ hole; Current pressure limits are to be 300 PSI. Dimensions can change slightly to suit the bonding process.
Can you quote this project? We will typically want 300 Units batches.
Thanks
Jack Marrelli
281 217 3417
we are planning to bond Metal/alloy housing to Alumina or Glass ceramic. I would like to understand the required bonding metallurgies as well as process. Thanks..Kishor 4082026088
Hello,
I would like to get more details regarding bonding a thin PZT sheet to an Aluminum sheet.
What are the main parameter in the bonding procedure?
Hello your technology sounds awesome, but… have you an adhesive to ceramic-steal, up to 750°C?
I would like to explore the possibility of bonding a ceramic layer to a stainless steel surface. Is there anyway I could be contacted to discuss this further?
Please contact us at info@s-Bond.com
Hello,
I wish to bond ceramic (piezo) to some metal without loosing the electrical conductivity. Any feedback would be appreciated.
Thank you.
Yes… S-Bond 220 and 130 are processed below the Curie points and can join such piezo elements. Please contact us direct at info@s-bond.com for direct information.
Hello
I’m interested to learn more about your ceramic/metal bonding methods. Specifically I need to bond ceramic to copper but without exceeding the ceramic’s (PZT) curie temperature ( about 350C) in the process. In the context of piezoelectricity, the Curie temperature – Tc – of a material is the temperature above which the material loses its piezoelectric characteristics
Yes… S-Bond 220 and 130 re below the Curie points and can join such piezo elements.