Conventional soldering processes use chemical fluxes to remove the oxides from the molten filler metal and the underlying base metal surfaces that are being solder joined. In these processes, once the oxides are removed from the molten filler and the base surfaces, the molten filler wets and form a metallurgical bond. The problem with chemical fluxes is that they are corrosive chemicals and in any flux residue on the surface there is the potential of corrosion which is a long term reliability problem. Ultrasonic soldering is process solution that removes the need for corrosive chemical fluxes.
Figure 1 illustrates the ultrasonic soldering process mechanism employed a heated solder probe tip which is vibrated at frequencies from 20 – 60 kHz. Focused acoustic power in the specially designed tips initiates cavitation in the molten solder which remove oxides at the surface of the molten filler metal and at the surfaces of metals being joined. The molten solder acts as the acoustic transfer medium for the ultrasonic energy and as cavitation ( micro-bubbles) burst on all surfaces the action cleans the surfaces and exposes oxide-free metal that is immediately wetted by the surrounding molten filler metal.
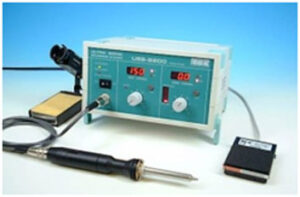
Figure 2 illustrates a typical commercially available ultrasonic soldering iron. One should note that ultrasonic soldering is not ultrasonic welding. Ultrasonic welding (bonding) employs higher pressure shear forces and does not have molten metal phase and is a high frequency shear force micro-friction welding process.

Ultrasonic soldering is very well suited as a mechanical activation process for fluxless soldering with S-Bond active solders. S-Bond solders rely on reactive elements such as titanium (Ti) and rare earth elements such as Cerium (Ce) to enable direct wetting of metals, ceramics and glass without the need for chemical fluxes or plating. However, active solders are not “self” wetting since their own oxides that form on melting create a barrier to the reactive elements in the molten solder. The cavitation from an ultrasonic solder iron tips disrupt these oxide films that form on the molten solder. Figure 3 illustrates how an ultrasonically activated heated tip enables the active solder fillers to wet and adhere directly glass. The same process enables active solders to wet and bond to works on all metals and ceramics.

Ultrasonic soldering tips can be narrow and suited for soldering narrow lines and/or point soldering as shown in Figure 4, or larger heated ultrasonic horns (Figure 5) can be used to activate a much larger area to deposit an active solder layer as the first step in soldering two surfaces together with an active solder.
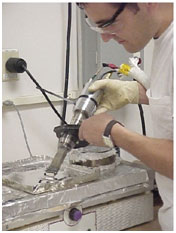
Ultrasonic soldering of active solder is an excellent high volume production process. Figure 6 illustrates a wire fed robot operated soldering iron that can be used in spot, line or large area ultrasonic activation of active solders.
Ultrasonic soldering is growing in application with the ever increasing use of dissimilar materials and where many soldered assemblies need to eliminate the use of corrosive and contaminating fluxes. Also ultrasonic soldering and active solder permit the precise placement of solder filler metal.

For more information on ultrasonic soldering and for an evaluation of how ultrasonic soldering can help you application, Contact us.
One Response
Dear Sir
Please give me an offer for Ultrasonic Soldering Station
Best regds