Ultrasonic Assisted Solder “Welding”

S-Bond Technologies have demonstrated a process for making “active solder filler metal” joints and seals on aluminum assemblies. The process is similar to MIG welding processes which use higher melting temperature filler metal wires fed into a moving arc to create a weld fillet. In Ultrasonic Assisted Solder “Welding”, an ultrasonic solder tip is a heat source to melt the solder wire, instead of a welding arc. The heated tip melts S-Bond 220 wire solder which is continually fed to the solder tip, as seen in Figure 1. For aluminum soldering it is suggested the area of the joint be heated to the solder melting temperature using supplemental heat sources to provide a stable molten pool for the ultrasonic activated tip to run.
The solder iron tip is “drawn” through a molten solder bead on the heated aluminum component faying surfaces (190 – 250C) in order to deposit a solder bead that through mechanical activation wets and adheres to the underlying aluminum. This ultrasonic assisted technique enables the active S-Bond solders to directly wet and bond to the underlying aluminum surfaces without the need for an aggressive chemical flux.
Figures 2 and 3 illustrate the Ultrasonic Assisted Solder “Welding” process on a tube enclosure and on butt joint for aluminum sheet. In these applications the component surfaces are heated and the active solders are melted and applied via the heated soldering iron tip to form a molten bead at the joint. The ultrasonic soldering iron tip is submerged in the bead and mechanically disrupts the oxides on the active S-Bond solder. Due to the active elements in S-Bond, the ultrasonic gitation of the solder tip enables the solder to directly wet and adhere to aluminum and many other metals.
Figure 4 shows an actual Ultrasonic Assisted Solder “Welding” process in operation as it forms a joint between two aluminum sheets.

Figure 5 illustrates the mechanism of how an ultrasonically activated heated tip enables the active solder fillers to directly bond to most metals. The figure illustrates how an ultrasonic soldering tip creates cavitation (intense bubbles) in the molten solder which disrupts oxides that have formed on the molten solder and the joint surfaces. The cavitation in effect, cleans and mechanically fluxes the soldering area. The soldering tips are driven by a power source that excites the ultrasonic soldering horn at 12 – 25 W of power and a transformer to resistively heat soldering iron tip. Figure 6 is a picture of typical ultrasonic soldering equipment.
Ultrasonic soldering is very well suited as a mechanical activation process for soldering with fluxless, active solders such as S-Bond. S-Bond solders rely on reactive elements such as titanium (Ti) and rare earth elements such as Cerium (Ce) to enable direct wetting of metals, ceramics and glass without the need for chemical fluxes or plating. Ultrasonic “solder welding” is an extension of this principle that can be used to make joints and seal in aluminum assemblies without
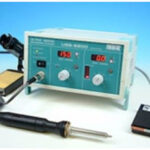
having to use conventional aluminum welding which might distort or “burn though” thinner aluminum structures.Active solders are versatile at joining and sealing many different types of assemblies. Ultrasonic solder welding is another example of how S-Bond Technologies adapts processes to provide bonding solutions.
Contact us to evaluate how ultrasonic solder welding or our other bonding solutions can be used in your applications.